How can we turn our nose up at the use of plastic in modern cars?
Let’s go back in time and start with the one of the pioneers for the use of plastic in car exteriors, the Trabant.
We begin this journey on the Soviet side of the Berlin Wall.
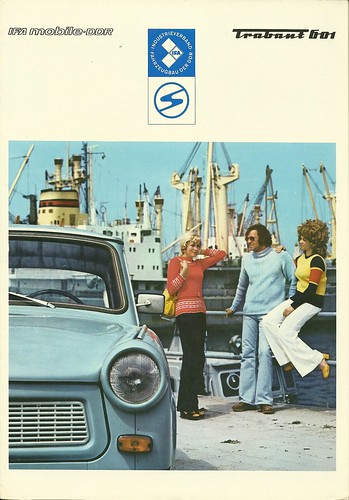
“In 1957, the Trabant started out as East Germany’s answer to the VW Beetle as the people’s affordable car. It was simple design that could easily be maintained and repaired by its owner using a few basic tools. Most owners carried a replacement belt and sparks plugs at all times.
The first Trabant, a P 50, was powered by a smoky two-stroke generator that maxed out at 18 HP; the P was stood for plastic and the 50 signified it’s 500cc engine that used only 5 moving parts. To conserve expensive metal, the Trabant body was manufactured using Duroplast, a form of plastic containing resin strengthened by recycled wool or cotton. Surprisingly, in crash tests the Trabant actually proved to be superior to some modern small hatchbacks.”
(Source)
It sounds great, I wouldn’t mind one myself, but hang on a minute. What’s Duroplast? Duroplast is a composite thermosetting plastic, and it’s made by mixing plastic with cotton or wool fibres. Thermosetting plastics are renowned for being scratch-resistant and shock-proof, but they are quite heavy. It’s not really used much in modern day, but the most similar thing you will find is fibreglass. If the Trabant performs as well in crash tests as ‘some modern small hatchbacks’ then why aren’t we using Duroplast now? For the concern of vehicle plastic recycling, it’s simply a no-go.
Duroplast – a thing of the past?
Duroplast cannot be recycled, which is a shame, as it’s strength and mould-able nature makes it comparable to steel. Modern innovations have been implemented to dispose of the Trabants, of which an estimated 3% of the original three million produced are still on-the road-today. Some of the vehicles are stripped of everything except the Duroplast, and shredded down, added to concrete and used in construction. This is performed by the same factory that produced the cars originally, I guess that’s a kind of vehicle plastic recycling, right? Alternatively, some are treated with a new Biotech solution that effectively disintegrates the chassis in just 20 days.
The Trabants are the butt of a long standing joke about conditions in Eastern Germany before the Berlin Wall fell in 1989. Now, they are a historic memento of the methods used in old car production. Kudos must be given to using plastic as an alternative, as now almost all cars use plastic in their exterior, not exclusively, but for the properties that differ it from metals.
Practical Plastic Parts
Motoring writer Iain Dooley has stated “Ideally the car should be viewed more as a commodity or a tool to get whatever job you need to do done. If this view was more widely adopted maybe the need for glossy metallic paints and fancy alloy wheels would diminish.” This leads me into my next point, using plastic in cars is practical, but not particularly aesthetic. Using plastic instead of metal or glass is beneficial for fuel economy, as the lighter a car becomes, the more miles per gallon can be squeezed out. It also increases the use of vehicle plastic recycling, a great way of continuing and promoting the circular economy; metal may sit and rust for years in a junk-yard.
The benefit of using plastic for car bumpers is the simplified nature of their complicated manufacturing, it’s easier to instruct a computer to design the plastic build. Most often the point of contact for a collision is the front or rear bumper, and so they are designed for this purpose. Inside the bumper is an intricate design that allows the bumper to crumple, rather than shatter, or crack. Plastic can’t take all the credit, as it is a combined effort of polymers and metals to create an effective crumple zone, which save countless lives by absorbing energy in crashes.
Now, let’s have a look at the Citroen C4 Cactus (see below), which has introduced a new motoring technology known as Airbump®.
“The Airbump® panels are a global exclusive that blend quirky style with innovative function. They protect your car from minor everyday bumps and scrapes, while adding to your Citroën C4 Cactus’ unusual, eye-catching design.
The clever Airbump® panels are made from supply TPU (Thermoplastic Polyurethane) and include tiny air capsules that absorb impacts and help prevent scratches. They don’t need any maintenance and help cut costs from small scratches and bumps.”
Let’s talk about the content, Thermoplastic Polyurethane (TPU), a highly desirable manufacturing polymer. Ideal for it’s elasticity, scratch resistance and strength, TPU is used for all sorts of production purposes. It can be found in shoes, sports equipment, power tools and even mobile phone cases. For the Citroen C4 Cactus, it is an ideal introduction, as it’s too common an occurrence for your car door to get paint chipped by careless neighbours. Just the other day I saw a woman open her car door into the next car, leaving a small dent and paint chip, and I thought ‘there must be another way’. The Airbump® panels are not only on the side of the car, but on the rear and the front corners. Considering vehicle plastic recycling, TPU can be reused for durable products like handrails and scaffolding. I for one, am interested to see if Airbump® catches on, and how many other new plastic innovations can be invented.
To see what we can do with Vehicle Plastic Recycling, follow this link
In a new BBC TV Series, ‘James May’s Cars of the People’, James May discovers how cars become a normal part of every day life. Click here to see episode one on iPlayer.